As creative as we are with our sewing skills, sometimes we also have to get creative with our sewing space. A large, dedicated sewing room is every sewist’s dream, but finding the perfect sewing furniture for small spaces can be challenging, especially if it needs to blend with your living room, dining room, or bedroom decor and may need hidden away when not in use. Your local sewing store will usually have wonderful choices, but we also found some other sources for multifunctional spaces.
Sauder Craft and Sewing Armoire
When the doors are closed on this armoire, it’s just a stylish cabinet in your room. Open the doors to reveal a slide-out table for your sewing machine and 6 adjustable shelves to use for storage and comes in several different finishes to blend with your decor. The armoire is available from various online resources such as Home Depot, Walmart, Amazon, and more. Visit the Sauder website to see all of their furniture options. Assembly required.
If you purchase from one of our Amazon links, we may earn a small commission at no additional cost to you.
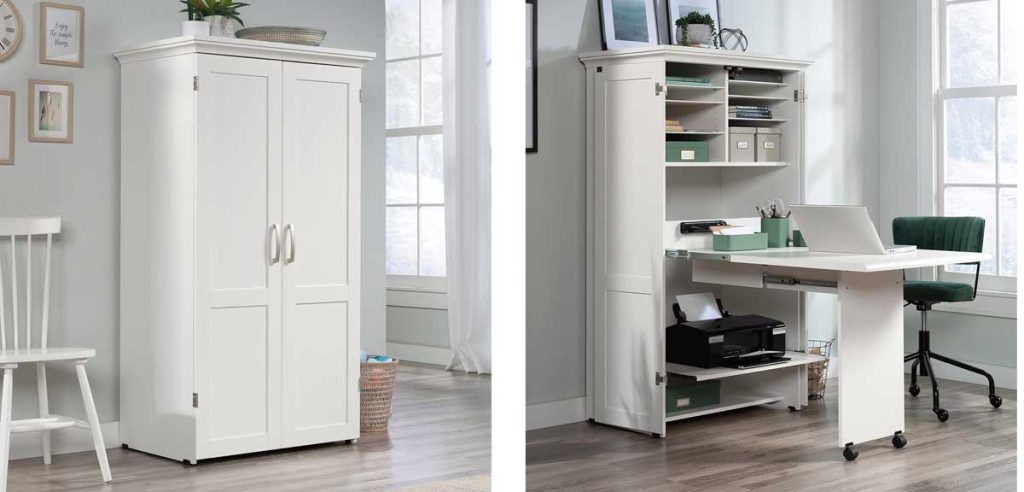
IKEA
IKEA, known for its affordable furniture, offers possibilities for creating a customized and efficient sewing space with pieces that can be repurposed to create a work area that suits your needs.
- Foldable NORDEN Gateleg Table: Maximize space with the NORDEN gateleg table. When folded down, it’s compact enough to sit against the wall, but when expanded, it offers a large workspace for cutting fabric or as a work area. Mounting casters to the bottom enhances mobility and flexibility. Comes in white or birch.
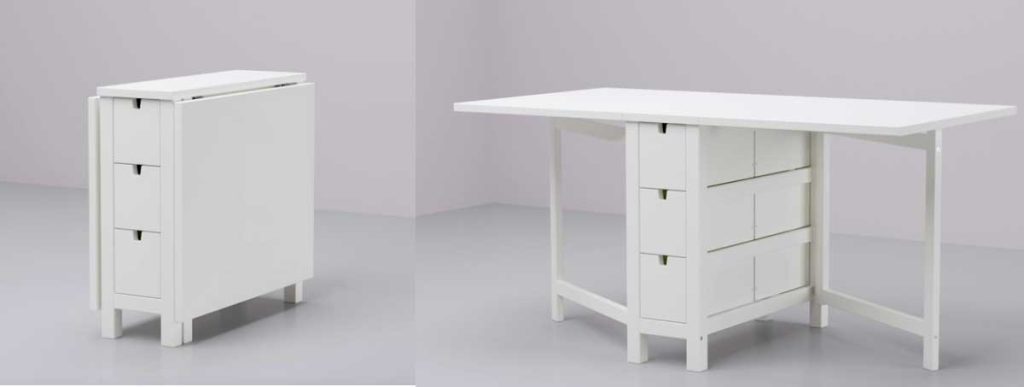
- LINNMON tabletop and ALEX drawers. Combine two or more ALEX drawer units as table legs, then place the LINNMON tabletop on them. This creates a sturdy and spacious surface for your workspace.
Better Homes & Gardens Modern Farmhouse Sewing Table
When this cabinet is closed, your machine and storage areas are hidden and the extension folds down flush to the cabinet. It takes up a small footprint and looks like a small sideboard in your room.
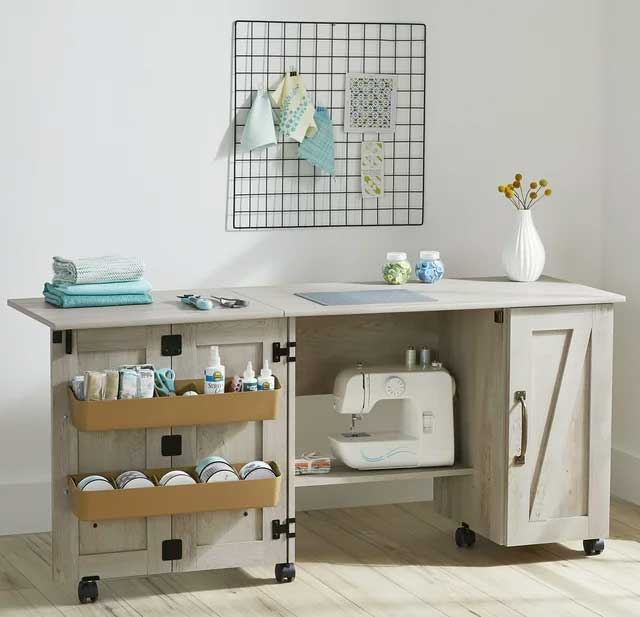
DIY with Lumber and Paint
This sewing station can be made with DIY products from a big box store, or with pre-fab bookshelves. Add an MDF or laminated top and paint in your favorite color. Tip: some bookshelf units (including the BILLY bookshelves from IKEA) have doors available so that you can hide your supplies.
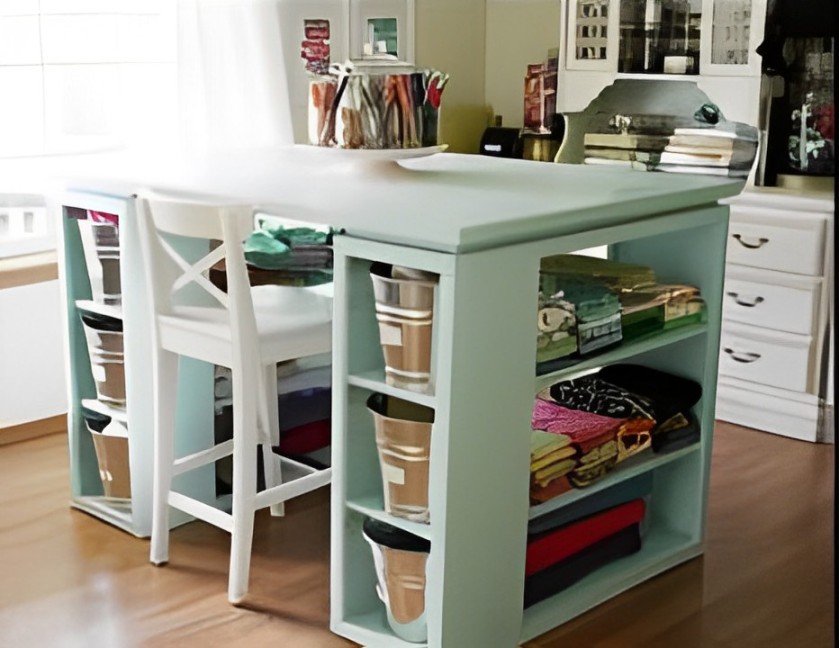
Slide and Hide
Small spaces need big solutions. “Cabinet filler” organizers are often found in the kitchen next to a wall or refrigerator. They can be wide or narrow and easily slide out on wheels to quickly choose what you need, then slide back in to be hidden away. These cabinets offer plenty of storage in a small footprint and can easily be customized with one or more sliders as needed.

Whether you’re a seasoned seamstress or just starting out, organizing your sewing space to what’s comfortable for you and to what fits in your budget and home is key to unlocking your creativity and maximizing efficiency. Hopefully, these ideas will help you turn every project into a satisfying and enjoyable journey!