Q: I want to make a coat from faux leather and wondering how to make a buttonhole in this fabric.
A: Faux leathers come in a variety of styles and textures, but generally they have some kind of knit backing to stabilize the textured vinyl front surface. If yours does not, then use small dots of textile glue inside the seamline to place a sturdy interfacing behind the buttonhole area. If you don’t interface the area, the buttonhole will never return to its original size after use.
To sew a machine buttonhole in faux leather, check to see if your machine has a special buttonhole stitch for the fabric. The one shown in the photo is specific to leather-like fabrics. The stitch shown is actually sewn after the buttonhole opening is slashed so that the stitch goes over the raw edges. A sturdy bartack at each end prevents distortion.
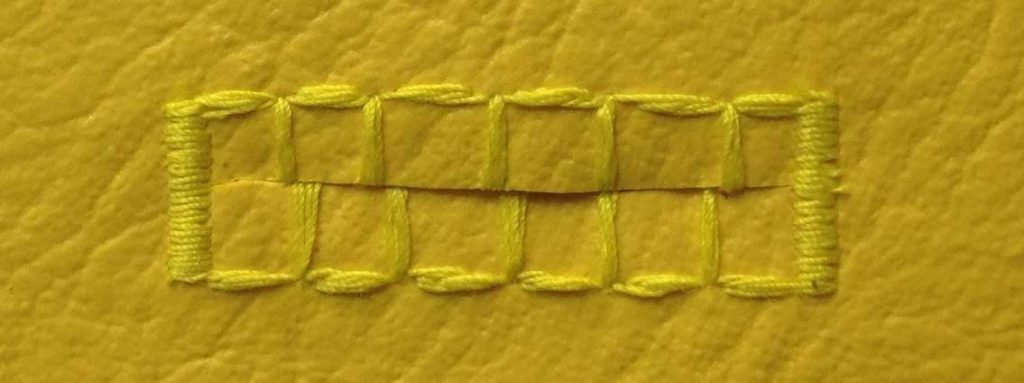
Another type of buttonhole suited to faux leather has a straight stitch along each side of the hole location, and there’s a wider space between the stitched lines. Since faux leathers don’t ravel, the stitching just helps the buttonhole area keep its shape.
It’s a good idea not to use a traditional buttonhole on most faux leathers, as the close satin-stitched bars can perforate the fabric. So, be sure to test-stitch.
No matter what buttonhole type you choose, if the machine foot doesn’t feed evenly and sticks to the fabric surface, use a piece of water-soluble stabilizer under the foot for even feeding.
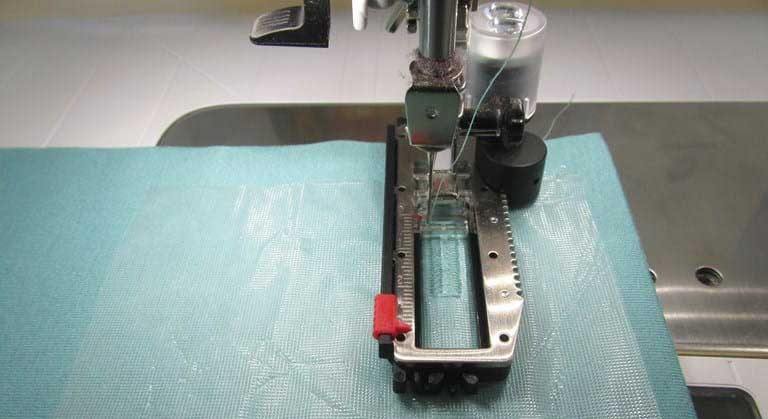
Q: I’m making an apron and the pattern calls for the binding to be cut on the bias. Since cutting on the bias takes more yardage, is it really necessary to cut it that way or can I just cut crosswise strips for the binding?
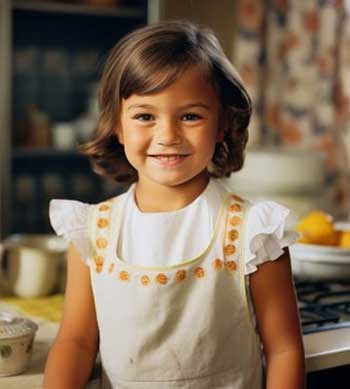
A: The answer depends on the apron itself—are parts of the bound area on a curve, like armholes or bib edges? If the answer is yes, then you will need to cut the binding on the bias so that it can shape to the curves, as straight-grain binding will not curve properly. If you try to shape straight-grain binding to a curve, you will get pull lines or puckers.
Many sewers like to cut their binding on the bias as a design feature. If the binding fabric is striped, cutting it on the bias creates a decorative diagonal patterning, as opposed to simply crosswise lines.
Note that you can piece bias binding in multiple places to use less fabric than cutting much longer strips at a 45° angle. If you match the patterning at the diagonal seam, no one will be the wiser and the seam will be almost invisible.
Q: What’s the best way to pre-treat fabric before I sew It?
A: The general rule for fabric you’re sewing, is to pre-treat it as it will be cared for once the garment or project is finished. The answer really depends on the type of fabric and what you plan to use it for.
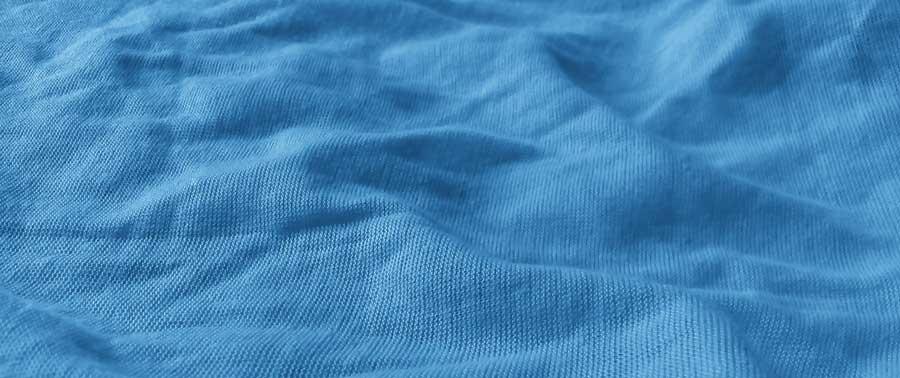
If it’s 100% cotton fabric, there’s a chance for some shrinkage. If you’re using that fabric for a quilt, shrinkage may not be a concern, but if you’re using it for a garment, shrinking could be a definite issue. Some cotton fabrics, like flannel, can shrink significantly, causing your garment not to fit after washing. Denim should be washed and dried multiple times as the fabric often has residual shrinkage.
Follow the care instructions on the bolt end to pre-wash any cotton or cotton blend fabrics to avoid two things—shrinkage and color transfer. The latter occurs when a bright color is next to a lighter one—think red hearts on a white background. After washing, the background can become light pink, depending on how the dyes are set. If that happens, rewash with a color catcher to capture the excess dye.
For most synthetic fabrics, like polyester, there is no need to pre-treat, as shrinkage isn’t an issue. If you’re concerned about any applied finishes, pre-washing is an option.
For dry-clean-only fabrics, like wool and wool blends, it’s best to at least thoroughly steam the fabric before use to help avoid shrinkage, or to actually send it to the drycleaner before cutting out your garment and ask them to steam it.
Home décor fabrics generally do not require any pre-treating, as they often have stain-repellant finishes that can be removed by washing.
~Linda Griepentrog is the owner of G Wiz Creative Services and she does writing, editing and designing for companies in the sewing, crafting and quilting industries. In addition, she escorts fabric shopping tours to Hong Kong. She lives at the Oregon Coast with her husband Keith, and three dogs, Yohnuh, Abby, and Lizzie. Contact her at .