It’s Stripe Hype!
Whether you’re binding a jacket front, collar or a quilt, using a striped fabric for the binding is a great way to accent the edge.
Stripes come in varying forms—from simple two-color versions to multi-color patterning, wide to narrow—but one thing’s for sure: they’re fun!
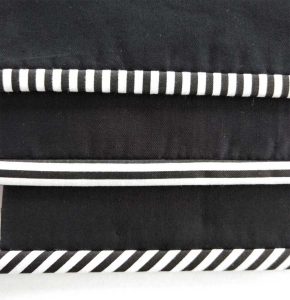
Stripes can be used three different ways for binding an edge: lengthwise, crosswise or on the bias. The choice depends on the desired finished look.
Using a stripe lengthwise on a binding showcases only about ¼” of the patterning, so for wide stripes, this use really isn’t a good option as you’ll likely see only one color. However, for tiny stripes, you can showcase three or four lines. Using a stripe lengthwise requires more yardage than cutting crosswise and/or more frequent seaming. You can use the entire fabric width and less yardage, but that strategy requires more seaming and matching end to end. The fun part—you can decide which stripes to showcase, but remember you’ll need to allow for seam allowances, so place the featured stripes accordingly.
Cutting binding crosswise is another option that showcases stripe repeats at right angles to the project edge. It allows for more visibility of stripe patterning and fewer seams are required with less yardage.
Many stripe aficionados prefer to cut striped binding on the bias (a true 45° angle) for some diagonal interest. The amount of yardage required depends on how frequently you want to piece the strips, matching the stripes. Cutting striped binding on the bias allows it go smoothly around curves, which is not the case with the horizontal or crosswise cutting, as those grains are suitable only for straight edges (like most quilts) rather than curves.
Piecing
In almost all instances, unless you have a short edge to cover, binding needs to be pieced to make enough length for the project. It can be pieced in two ways: with diagonal or horizontal seams.
Diagonal Seaming: While diagonal seaming makes for flatter binding because seam allowances are offset and not on top of themselves with multiple layers, it can be more difficult to align stripes with this bias seaming.
Crosswise Seaming: For crosswise stripe fabric strips, it’s easier to get a more invisible seam if you use horizontal piecing, sewing strips end to end. This technique also allows for a regular repeat of the stripe. To create a horizontal seam, place strips right sides together matching the same stripe on both layers. Stitch down the center of the stripe, trim the seam allowances to ¼” and press open. If you stitched accurately, the seam should be almost invisible and show a continuous stripe pattern along the binding.
Finishing
Once you’ve pressed your binding in half and sewn it the edge, first press it toward the edge you’re covering. Then fold it to the underside and hand-stitch the folded edge of the binding to the back side of the garment, quilt, etc.
For a quicker finish, fold the binding to the underside, pin or clip securely so that the underlayer is slightly wider than the top binding, and stitch in the ditch of the seamline where you initially attached the binding. Because the binding underside is slightly wider than the top, your stitching should easily catch the folded edge to secure it. Using transparent thread (either smoke or clear) works well for this, especially if your project is multi-color.
~Linda Griepentrog
Linda is the owner of G Wiz Creative Services and she does writing, editing and designing for companies in the sewing, crafting and quilting industries. In addition, she escorts fabric shopping tours to Hong Kong. She lives at the Oregon Coast with her husband Keith, and two dogs, Yohnuh and Abby. Contact her at .