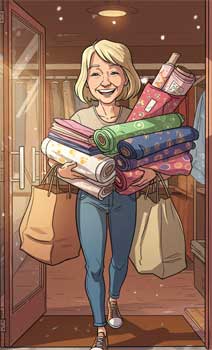
I’m happy to share with you that I am indeed a fabricholic. My husband claims that we have an inventory control problem. He means that the fabric comes into our house faster than it becomes something and goes out. And (my husband says) I also live under the delusion that fabric instantly becomes a project or a garment-without any labor on my part. In fact, I often buy fabric to go with things that I have, like shoes and jewelry. Unfortunately, the shoes wear out while the fabric still sits there waiting to become something.
Fabricholism manifests itself in a variety of symptoms. You don’t need to raise your hands or openly confess… but think about your answers to these questions!
- Do you purchase fabric whether you need it or not?
- Do you have more fabric than you could comfortably sew in __ ? A week? A month? A lifetime?
- Have you ever said “I’m not going to purchase any more fabric until I sew up what I have”?
- Do you have fabric under the bed? In closets? Under garments that are hanging on hangers in your closet?
- Do you have patterns that you’ve never used?
- Have you ever purchased any patterns for your daughter… who now has a granddaughter?
- Did you ever buy more fabric than you intended when you went to a fabric store?
- Have you ever refused to purchase a ready-to-wear garment because you thought you could make it cheaper and better?
But, I NEED it!
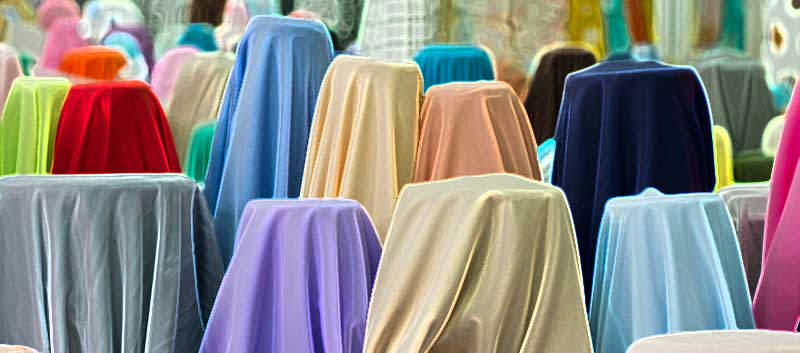
As a fabricholic, I can offer many rationalizations for buying fabric.
- Buying fabric is hedging against inflation. You know that the price can only go up.
- If I don’t get it, somebody else will.
- Stuff always looks better on the cutting table than it does on the bolt.
- Buying fabric is cheaper than psychotherapy. It’s not immoral, it’s not illegal, and it’s not fattening. Fabric has no calories!
- I don’t have any other bad habits. I don’t drink; I don’t smoke; and the question of whether or not I overeat depends on what I’m wearing on any given day.
- Buying fabric is environmentally safe and proven to be helpful to the recycling industry.
- Fabric has good insulating properties.
- I view collecting fabric as an historical thing, like charm bracelets or postcards. I have traveled extensively and have always tried to buy a piece of fabric in each city. When I get home, I can sit on the floor of my sewing room, look in my closet, and bring back memories. It’s like scrapbooking in a different form.
- From my mother I inherited the idea that if you keep something long enough, it comes back in style. Vintage fabric happens to be “in” and depending on your age, vintage fabric makes its own definition.
- Buying fabric gives you a sense of social responsibility because you are actually keeping people employed at those stores.
- Fabric is easy to care for. It doesn’t require refrigeration. You don’t have to cook it, feed it, water it, wipe it, or walk it. It’s low maintenance compared to other things you might have around the house (commence staring at your children).
- If it’s on sale, that’s a good clue that you should have it.
- Your friends made you buy it.
- It’s good when you think of yourself as being worth this purchase—it reinforces your ego.
- If you move frequently, fabric can become good packing material.
- Everything in the fabric store fits you.
- And my favorite: “God wants me to have this!” How do I know that? Because I looked at it a few days ago and it’s still here. And there was a parking space right in front of the store.
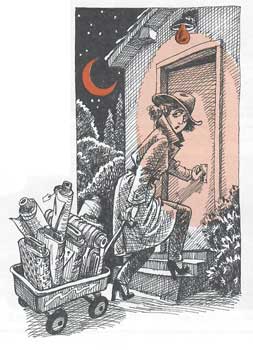
You have to decide if you are going to feel guilty about this whole scenario or just go with the flow and say “I am a fabric collector.” There are people who collect stamps; there are people who collect coins. You collect fabric for what it is. You don’t have to have an intended use.
Being a fabricholic is not a bad thing. We all have wonderful friends who share our passion and it adds a lot of enjoyment to our lives. Recognize that collecting fabric and sewing fabric should be considered two separate activities. Sometimes they’re not even related!
~Linda Griepentrog is the owner of G Wiz Creative Services and she does writing, editing and designing for companies in the sewing, crafting and quilting industries. In addition, she escorts fabric shopping tours to Hong Kong. She lives at the Oregon Coast with her husband Keith, and three dogs, Yohnuh, Abby, and Lizzie. Contact her at .