Creating wearable art satisfies the desire for something special to wear, the craving you feel to express yourself, and a reason to use the luscious fabrics and threads you just bought. Now, what to make? Why not create a garment that takes you to a land far away… to an exotic place of serenity and ancient culture… to a place where style is timeless, tradition is honored, and nature is the essence of life? Creating wearable art with Asian flair allows you to fulfill that fantasy. Just select a simple pattern, colors that appeal to you, fabrics and motifs that inspire, and sewing techniques to embellish. Collect your treasured items and find some time for yourself.
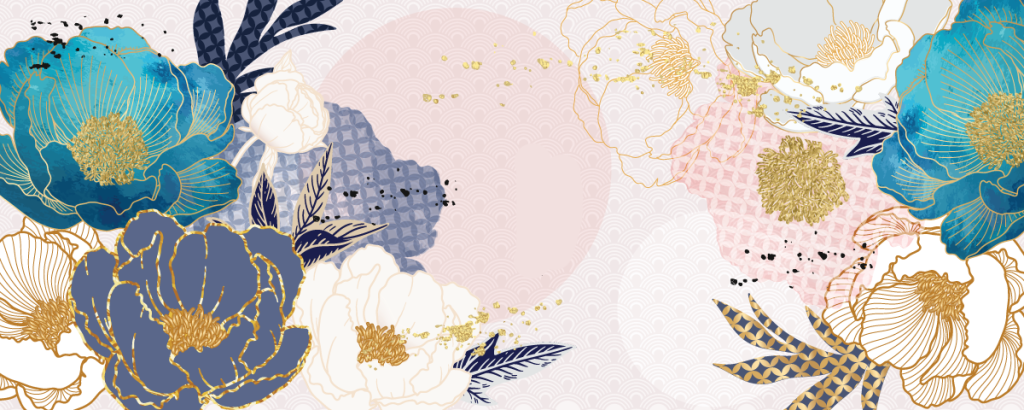
The full article is in the Members area of the website. CLICK HERE to read the full article. Not a member? Join online!