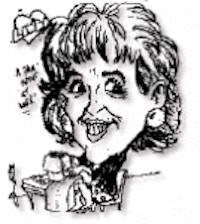
ASG is excited to announce that international designer Linda MacPhee will be the keynote speaker at the 2020 conference in San Antonio. As our way of introducing her to you, we have selected her as our independent designer of the month for February. Linda hails from Alberta, Canada and will be once again making her way back to conference.
Sears Catalog for Inspiration
As number 5 of six kids and raised on a family farm in northern Alberta, money wasn’t abundant. In fact, her early memories include going through the Sears catalog with her siblings and picking out their favorite outfits, only to have a local seamstress try to duplicate them from old garments. Even then she realized the finished product never really did live up to the picture she had chosen and hoped for. That’s why she decided at an early age to try her own hand at sewing. She sewed her first garment when she was about 12 when she wanted a new dress for her cousin’s wedding. “My dress was quite successful I remember; but because I knew nothing of fitting, I had to position myself against a wall so I could use my one hand to hold/grab a handful at the back of the dress to make it look like it fit! I guess that dressmaker likely influenced my desire to create my own look. Looking at family pictures now she really was a master as my brothers were in good looking suits that she had recycled from whatever. My mother didn’t sew or have any interest in sewing, although I’m sure she must have mended and repaired things as necessary. Our dressmaker, Mrs. Schmitt, was from Germany and was truly a master at the sewing machine. (We had a treadle of course!)”
Concerning her formal training, Linda commented, “I joined the local 4-H sewing club when I was old enough and that was my only training until I graduated from high school. I enrolled in Home Economics at the University of Alberta as by that time I was sewing all my clothes and was interested in learning more.”
It Started With a Parka
While working as a district Home Economist for the Department of Agriculture (extension agent) in Northern Alberta and at one of her meetings with 4-H groups, Linda met a leader who had on a beautiful Parka. She was a nurse and had recently immigrated from the Phillipines. While chatting, Linda learned that the woman had made it herself. That set her mind in motion and she set about to make one herself. It was no easy task for the woman had tanned her own coyote skin for the fur trim and had sourced her own fabric (wool duffle) from the local Hudson Bay store. Linda explained, “Well, I didn’t tan my own skin but decided if she (a nurse) could do it so could I—a Home Economist! So I did!! My favorite childhood story that I had read to me many times was “The Little Red Hen,” and the theme has fulfilled itself many times in my life!”
She continued, “One of my responsibilities as the extension agent was to teach adult sewing classes to rural women. I met lots of people and with my parka on, came many requests to make them for people. I had learned also how to make moccasins/mukluks from some of the Native American ladies I had worked with. So in my spare time I started making parkas and matching mukluks for a never ending line up of customers. I charged them $100 which seemed pretty good at the time! I realized quite quickly that the demand would never end, so I decided to teach people how to do it themselves. That was the start of my business!”
The Inuit ladies of the N.W.T. had been making parkas for years so those parkas were the inspiration for the basic design. Wanting her parkas to be different, she added applique and trim, and each one became its own work of art. She came up with many different patterns for parkas and applique designs to help people come up with their own look.
Creating the World’s Easiest Patterns
In commenting on her patterns Linda added, “I have always wanted patterns to be simple, “not rocket science.” I had basic pattern drafting from my university training, but my object was to have as few pattern pieces as possible and as simple construction as I could too. My object was to have everyone be able to make one of whatever I designed. My line of “world’s easiest” patterns were best sellers and business boomed. World’s Easiest meant the pattern was usually one, two or three pattern pieces total! I then taught an army of instructors to help in my quest to get everyone sewing. We then franchised our shops across Canada and life was good (but very busy). By this time I was married and my husband who was an R.C.M.P. officer turned down a transfer and joined the business full time which is the only way I could have carried on. Yes…. we are still happily married 52 years later!”
On the future of sewing…
“I’m seeing a renewed interest in recycling coming from the younger people, and that I find so exciting. They have inspired me to recycle/recreate, and I have made many patterns to help with this aspect of sewing. Once this group discovers the potential of the sewing machine, they will be hooked! This direction has brought me full circle to my humble first attempt!”
In her quest to teach the world to sew, she decided the best way to do it was by having her own T.V. show. It was quite a task to get going but she and her husband managed and directed “Sew Much Fun” and ran with it for 6 seasons (72 shows) which showed on Canadian channels as well as PBS in the U.S. They then developed that into “Linda Macphee’s Workshop” which ran for another 6 seasons. “That was likely the highlight of my career,” she added. “I was awarded the “Woman of Vision” by CTV Television and YWCA “Entrepeneur of the Year” and also an “Award of Merit” from the Canadian government for Business. My alma mater, University of Alberta, awarded me their highest Distinguished Alumni Honor award.”
When asked about her favorite aspect of her job, she replied, “It is creating/designing the original garment and then seeing it through to a pattern to enable me and others to teach the world.”
However, she also reflected, “I have been saddened by the lack of Home Ec training in schools where I think the spark should begin! I never did take Home Ec. in school as my school was too small to have it. I, of course, did take it in University and did earn my teaching degree but opted to teach adults instead of youth.”
“If we can keep the world sewing, I think the future is bright. How you ask? I think the patterns have to be kept quick and easy. More sewing T.V. shows like mine would certainly help to show how easy it can be. For example…..in all the garment patterns I designed (well over 200) there was never a buttonhole in any of them. That was something that a novice might not do well, and my motto always was ‘make it look like you didn’t make it!’”
Being from Canada, Linda was never part of ASG as a member. She said, “I was a sort of member of the Holt Michigan group who I worked with/for many years. I very much enjoyed my work with many ASG chapters across the country. I was always promoting the formation of Canadian groups, but we just don’t have the population to make it work.”
Today Linda describes herself as “sort of retired” and only does “private gigs.” She has stopped doing major sewing shows, but loves doing her own version of fashion shows using local women as models for her garments. She spends her winter months in Mesa, Arizona and finds fun in doing smaller gigs for the multitude of retirement parks within driving distance. You can check out Linda’s patterns at her website at www.macpheeworkshop.com.
~Rosemary Fajgier