ASG Conference 2019 is over but the memories live on. There are so many conference highlights, but the topic of this article is the pleasure I had of interviewing Kenneth D. King on Thursday evening. The room filled with anticipation as the interview began. I had been working with Kenneth for months to prepare and the time was finally here. As we sat in front of the audience in our easy chairs, what unfolded was a fun “living room chat” filled with interesting tidbits and lots of laughter. Video of this event will be shared in the future, but that will take a little longer so, in the meantime, I hope you will enjoy these highlights. If you missed the event, you can at least get a taste of the great time we had spending the evening with Kenneth D. King.
Kenneth D. King
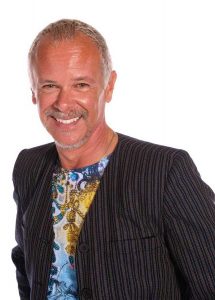
Kenneth D. King started his life journey in Salinas, KS. That journey has continued through OKC, San Francisco, and ultimately today, to NYC. He graduated Summa Cum Laude with a BS in Fashion Merchandising in OKC which launched his professional career. From there he moved to San Francisco to work in window display, but decided that he wanted his own business, which he started in 1986. His focus at that time was millinery.
After being in business for three years, he studied French Couture patternmaking for 9 months with Simmin (pronounced “Simone”) Sethna. His career began as a display manager in Oklahoma, but his true identity began to emerge and flourish after branching out on his own. Today we see him as an accomplished designer, adjunct professor, workshop teacher, author of 5 books and more articles and educational publications than I can count. He also has a novel, a podcast, and an audiobook to his credit. His work has been displayed in museums, seen on the red carpet, worn in concert tours, commercials, music videos, and highlighted in publications. His list of accomplishments is long and impressive. What a pleasure it is to spend time hearing from Kenneth D. King.
The Man Behind the Designs
How do you define yourself? Teacher, Designer, Author, or Other?
I’m a hybrid. I call myself a couture designer first, then a teacher, author, and storyteller. Over the years, I’ve realized that the central pivot of my career, has been—my craft. It’s been about making things, figuring out how to make things, writing about that, telling stories about that, teaching that, and entertaining myself and others with that.
More recently, as a writer, I’m embarking on another project—telling a particular story. I have the novel, which spawned the screenplay, and the podcast. Another project to add to my life.
Tell us about your latest book
And by the way, did you know we sold over 150 books for this event!
Why did you write it?
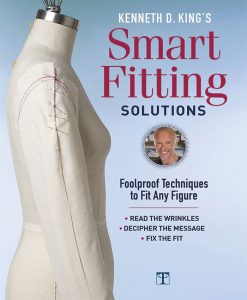
I wrote it because Judy Neukam understood better what was in my head than I did. She intuitively knew the information was far more useful, and also knew how to format it in such a way to give value to as many as possible. Also, since I’m a little lazy, she insisted. She also championed the project to the good people at Taunton.
What was the favorite part of the process?
Working with Judy Neukam.
The hardest part?
The fittings and muslins. That was a heavy lift—I did the main part of the sewing, before we photographed, and during, as we were generating the second and third muslins.
How long was this book in the works?
As I remember, it was at least 18 months, but may have stretched a little longer. Books have a long lead time.
Someone asked why you didn’t address pants in this book? Can you talk about that?
Fitting trousers is a whole other topic. For women more than men. Men have two basic shapes and are easier. Since women are more genetically diverse (men have blank spaces on the Y chromosome which explains so much), there is an infinite variety of hip shapes. Hence another book.
Over the Years
How have you seen your style/techniques change over time?
My early work was more structured, with more interlinings and such. My first wave was what I called the “embellishment” work. It was a particular technique that answered a question. I did an evening vest with embellished lapels, and that was my breakout hit—it got me out of retail. But I’m dyslexic, and needed a method to make the embellishments appear symmetrical. I hit on using yardage trim, because of a regular unit of repeat. Answering that question of symmetry made a body of work.
I moved onto sheer fabrics, because the inside is visible from the outside. So there were different questions I had to ask—like how to smock organza without the thread showing, or how to make a complex garment without seams or apparent seams. It’s answering the questions that develops the techniques.
What has shaped those changes?
Simple avoidance of boredom, that’s the easy answer. On a more complex level, I wanted to develop something that wasn’t there already. It’s a response to an experience I had years ago, when I got the see the collection of John Galliano in Paris that got him the job with LVMH.
Those Fabulous Hats!
Tell us the story behind the Elton John hats you designed.
I adored Elton as a teenager. So, when I started in my business selling to a store in L.A. called Maxfield, it was his lyricist Bernie Taupin who bought a vest first. I guess he saw it on Bernie. He went into the store, bought a vest, ordered more, and we were off and running. He has the really good pieces—accessories, hats, vests, dinner jackets, the first footstool. Each hat has a story, but the Diet Coke hat was exciting. He ordered a specific red—lipstick red—so I thought it might be for a specific project. The concert tour in 1988 was wildly exciting and scary—I had to tame a monster (the owner of Maxfield) first, though.
The Barbie Project
You have been involved with so many various projects. This next one looks like it was a lot of fun.
Tell us the story behind your recent Barbie couture project.
I got my start sewing Barbie clothes when I was four. So in January, my sister-in-law gently suggested that her granddaughter was Barbie age and might like some Barbie clothes. I bought a reproduction of the old-school doll, and started making clothes, and posting on Instagram. The fashion editor for New York Magazine saw them, contacted me, and asked me to replicate some looks from the collections for an article they were doing on Barbie as Influencer. So I got paid a whopping amount to make some tiny couture. Then it turned into a rabbit hole—I don’t see an end in sight. But jumping scale, as my friend Marshall says, made me re-think how things go together, as tiny clothes don’t construct like real sized clothes. So little Charlie is getting collections, birthday and Christmas.
On Display
You also have some of your work displayed in museums. Where are they? What are they?
I have work in four museums—an evening wrap at the Oakland Museum; three pieces at the DeYoung in San Francisco (hat, evening soufflé jacket, and black faille evening coat); The L.A. County Museum of Art (mermaid gown, couple of hats, couple of vests); and the V&A in London (an hat).
How did they end up being on display?
Some were gifted by me, some were gifted by clients, and some were gifted from estates of clients. A museum curator told me years ago that generally it was after 25 years in a client’s collection that they go into museums. That I have so many pieces there is good. I’ve been officially in business since 1987.
Strictly Entertainment
You also have another side to your creativity that veers into the entertainment business. I’m very interested to hear more about those creative avenues. You have a podcast, a novel and screenplay. How did you get involved in these?
I’m always looking to expand my horizons. Also, my second Saturn Return (age 60) was looming, and I was asking myself where to go next.
When I lived in San Francisco, I used to go to stand-up comedy, for enjoyment, as well as to observe and learn how they interact with an audience. After I moved to New York, I would go to what I call “Gay boy summer camp,” upstate. They always had a talent show, and a drag closet. So I decided for my talent to dress up and do some stand-up.
After one of these gigs, someone in the audience came up and told me I was good at it. He was a professional storyteller and said that I really knew how to tell a story. It occurred to me that I’ve been telling stories in class and to friends, so this seemed to be an avenue to follow.
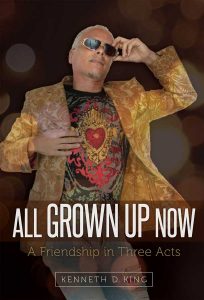
Listen to a personal reading from Kenneth D. King
The novel came about as a talking cure. In the mid-90’s, I had to help a friend out of an abusive relationship. It didn’t turn out like I had planned—it turned my life into a Fellini film for three years. Afterwards, I started writing to make sense of it. That turned into the novel, All Grown Up Now, a friendship in three acts. I self-published it after a frustrating round of talking to agents, them weighing in on what it should be, then saying they weren’t interested even if I changed it.
The novel brought forth the screenplay—it is act three in the novel. It was the story of going to Los Angeles to snatch my friend away, and what happened after. I’ve worked with a writing coach to refine it, and he has said it’s ready to shop around. I’m working with a woman who finds financing for films as well.
The podcast started as a way to get the novel in front of people—it’s the novel in installments. Episodes 1-29 are the novel, which I then turned into an audiobook. Starting with episode 30, people said I should continue, so I call it Season 2: Tales of a Checkered Past. This will one day morph into another audiobook.
I am enjoying the technique of telling a story with sound effects. I find the right sound effect can nail a pint or make a joke. This is an extension of studying stand-up; I listen to talk radio and observe how they use sound effects in addition to talk.
The podcast is also there to promote the film, to anyone who might be interested. It’s my way of telling this particular story to the world. That time in my life was huge—it really was a time where I learned a lot and stretched into a new area of life.
From Here to Where?
Where do you see these creative adventures going in the future?
Time will tell, but my aim is to have the film made, to tell this story. It’s about domestic violence in the gay community—something that isn’t talked about much. But domestic violence doesn’t have a gender, a social class, sexual preference—it’s just violence. It’s a universal story that just happens to be about two men. It’s also a tale of friendship—my friend Mark who got me out of Oklahoma, and how years later I got him out of that hellish relationship.
What should we be watching for next from Kenneth King? Anything new on the horizon you can tell us about?
Aside from pushing my projects forward, I have some articles for Threads Magazine coming out. This time seems to be one of gestation.
The Wisdom of Kenneth D. King
If you could leave us with 3 pearls of sewing wisdom, what would they be?
First—perfectionism is a disease. One can create the illusion of perfection, that’s the best one can do. It will never be perfect. Perfectionism is a form of fear—you can’t really learn anything from mistakes if you are obsessed with being perfect. Also, in my experience, perfectionists seem not to get anything finished.
This leads to the next bit—don’t be afraid of ruining a quantity of fabric, some good. It is the dues you will pay to be proficient. I had a student once who took 18 months to make a tailored jacket—as her first project. She was also a perfectionist. When she was finished (at my insistence), she was disappointed. She asked me how I got so good—my reply was that it wasn’t by taking 18 months on one piece.
Lastly, you don’t have to be good at everything. You just need to be good at what you want to make. That said, try new things, and try to be at least passable in other things.
A smart woman said to me years ago that if one is always at one’s best, one is, at best, mediocre. You don’t have to be brilliant at everything.
Oh. And make muslins!
~Sheryl Belson
Note: All images shared with permission